The Transformation of Metal Fabrication through High Pressure Die Casting Mould
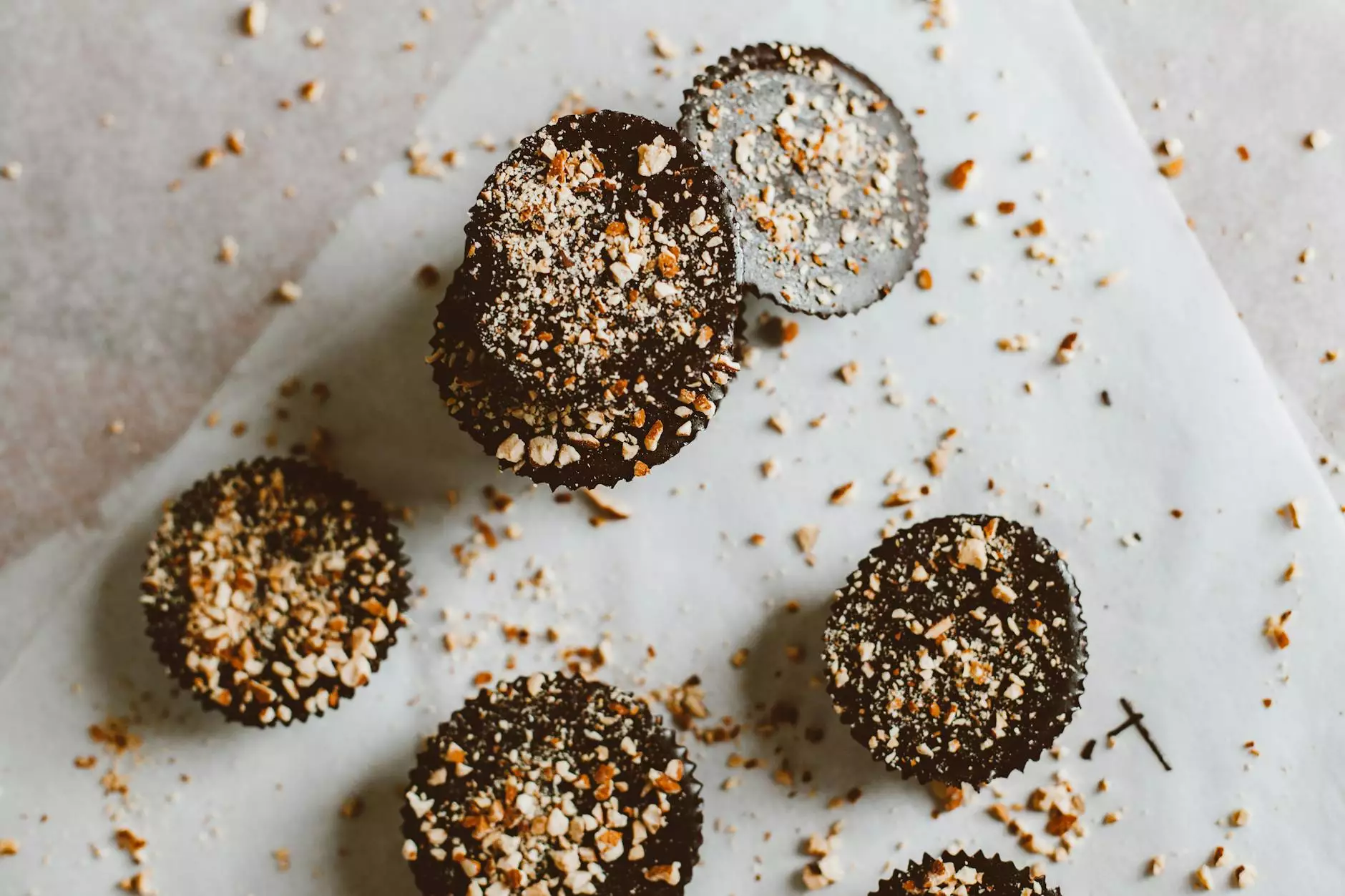
High pressure die casting mould has revolutionized the way industries approach metal fabrication, offering unparalleled precision, efficiency, and versatility. This process is integral to the manufacturing of a wide array of products, from automotive components to intricate electronic parts. In this article, we will delve deep into the world of high pressure die casting, explore its benefits, applications, and the future it beholds for businesses like those found at deepmould.net.
Understanding High Pressure Die Casting
At its core, high pressure die casting is a manufacturing process where molten metal is injected into a mold at high pressure. This method allows for the production of complex shapes with high precision, often eliminating the need for secondary machining. The key elements of this process involve:
- High Pressure Injection: Molten metal is forced into the mold cavity with great pressure, which ensures that even the finest details are captured.
- Rapid Cooling: The metal solidifies quickly due to the cold mold, leading to faster production speeds and reduced cycle times.
- Durable Moulds: The molds used in this process are typically made from high-quality steel or other robust materials, enabling them to withstand high pressures and repeated use.
The Advantages of High Pressure Die Casting Mould
Why should businesses consider implementing high pressure die casting mould in their production processes? Here are several compelling reasons:
1. Superior Dimensional Accuracy
The inherent nature of the high pressure die casting process allows for incredible precision in the final product. Tight tolerances and complex geometries are easily achievable, making it ideal for industries that require exact specifications.
2. Enhanced Surface Finish
One of the distinguishing features of high pressure die casting mould is the smooth surface finish it provides. This eliminates or reduces the need for secondary finishing processes, saving time and reducing costs.
3. High Production Rates
With rapid cycle times, a single machine can produce thousands of parts in a single day. This efficiency leads to decreased labor costs and maximized output.
4. Cost-Effectiveness
While the initial investment in mould creation may be higher than some other methods, the overall cost per unit dramatically decreases with high-volume production due to its efficiency and reduced waste.
5. Versatility in Material Selection
High pressure die casting accommodates a variety of metals, including aluminum, zinc, and magnesium, which can be tailored to meet specific performance requirements in various applications.
Applications of High Pressure Die Casting
The versatility of high pressure die casting mould has led to its adoption across numerous industries, including:
- Automotive Industry: Key components such as engine blocks, transmission housings, and structural parts benefit from the strength and lightweight nature of die-cast parts.
- Aerospace Sector: Critical components in aircraft, such as brackets and housings, require the precision and durability provided by die casting.
- Consumer Electronics: Enclosures for devices like smartphones, laptops, and appliances leverage the aesthetic and functional advantages of die casting.
- Healthcare Equipment: High-quality, reliable parts used in medical devices demand the accuracy and consistency achievable through this process.
Choosing the Right Die Casting Mould Supplier
Finding a reliable supplier for high pressure die casting mould is crucial for the success of your projects. Here are some factors to consider:
1. Experience and Expertise
Choose a supplier with a proven track record in high pressure die casting. Experience often translates to better understanding of the process and potential pitfalls.
2. Quality Assurance
Ensure that your supplier adheres to strict quality control measures. Certifications such as ISO 9001 are indicators of a commitment to quality.
3. Customization Capabilities
The ability to produce tailored solutions to meet your specific design needs is essential. This flexibility can significantly alter project outcomes.
4. Technological Advancements
The best suppliers are always at the forefront of technology, employing state-of-the-art equipment that ensures precision and efficiency.
Future Trends in High Pressure Die Casting
The future of high pressure die casting mould is bright, with several trends shaping the industry:
1. Sustainability Initiatives
As environmental concerns rise, die casting processes are being optimized to reduce waste and energy consumption. Innovations in recycling and material usage are becoming standard practice.
2. Industry 4.0 Integration
With the rise of automation and smart manufacturing, integrating digitally connected technologies with die casting processes will enhance productivity and precision.
3. Advanced Materials
The development of new alloys and composite materials is enabling manufacturers to produce parts with enhanced performance characteristics, extending the application range of die casting.
Conclusion
In conclusion, high pressure die casting mould represents a powerful tool in modern manufacturing, delivering exceptional benefits in terms of precision, efficiency, and versatility. As industries evolve and demands for high-quality metal components increase, embracing this technology through reputable suppliers like deepmould.net will ensure a competitive edge. Adopting these practices not only enhances product quality but also fortifies the future of your business in the metal fabrication landscape.
Understanding and implementing the strategies discussed above can pave the way for businesses to harness the full potential of high pressure die casting mould. Thus, fostering innovation and progression in an ever-competitive market.