Exploring Injected Molded Plastic in Metal Fabrication
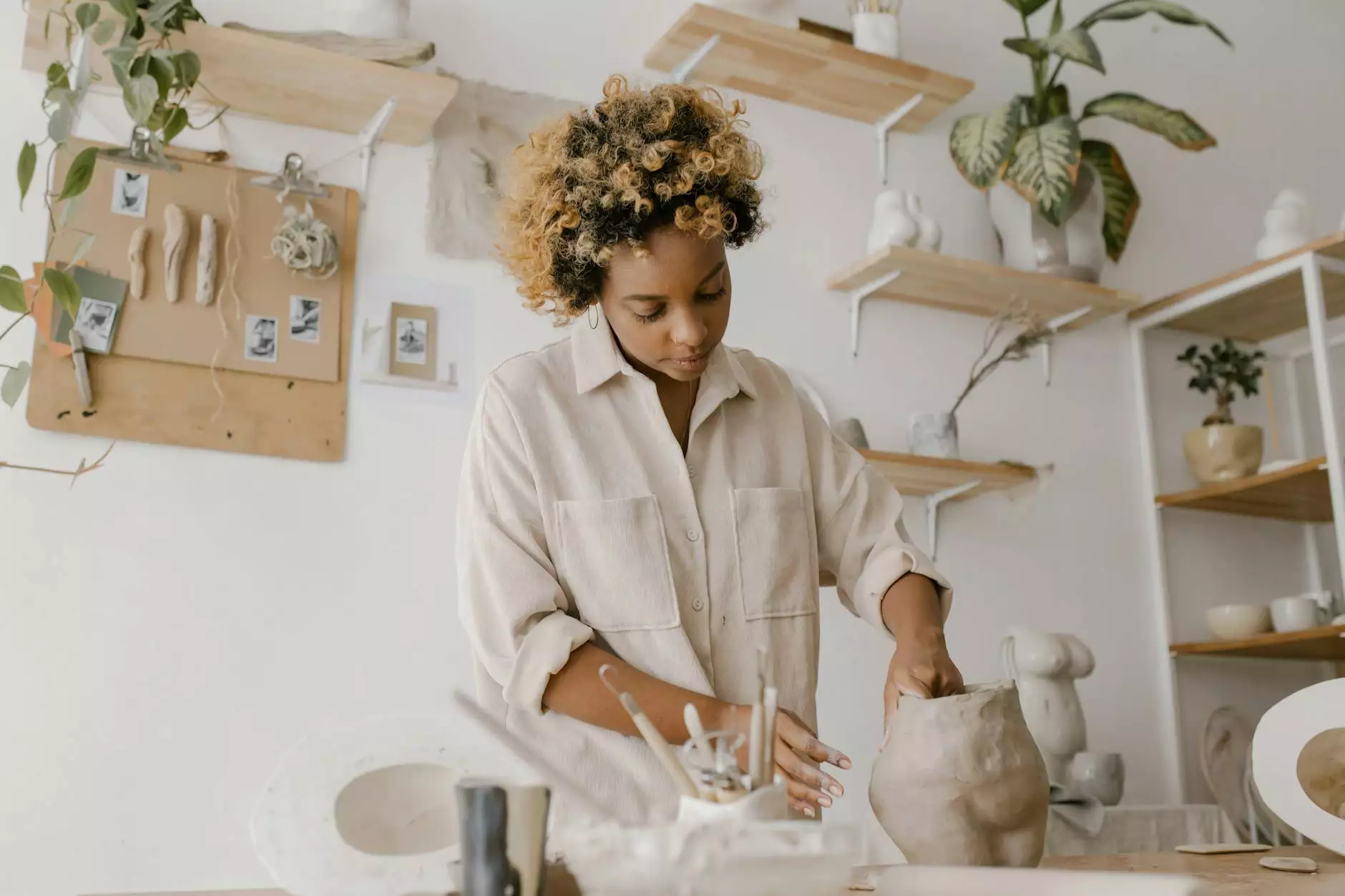
Injected molded plastic has revolutionized manufacturing processes across various industries. This innovative technology allows for the mass production of complex plastic parts with high precision and consistency. In this article, we will delve into the importance of injected molded plastic, its applications in metal fabrication, and how businesses can leverage this technology for superior product output.
What is Injected Molded Plastic?
Injected molded plastic refers to a manufacturing process that involves injecting molten plastic into a mold cavity. The process begins with heating plastic beads until they are liquid and then injecting this liquid into a mold where it cools and solidifies into the desired shape. This method is widely favored for its speed, efficiency, and ability to produce intricate shapes.
Advantages of Injected Molded Plastic
- High Efficiency: Once the mold is created, the production of parts is very fast, allowing for high-volume output.
- Design Flexibility: The ability to mold complex geometries makes it ideal for intricate designs that would be difficult or impossible with other manufacturing methods.
- Material Versatility: A wide range of materials can be used, including thermoplastics and thermosetting plastics, giving manufacturers many options to choose from.
- Consistency and Reproducibility: Parts produced via injected molding are uniform, which is crucial for industries requiring precise specifications.
- Reduced Waste: The process minimizes scrap and leftover material compared to traditional manufacturing methods.
Applications of Injected Molded Plastic
The applications of injected molded plastic are extensive and can be found in numerous sectors, from automotive to electronics. Here’s a closer look at some key applications:
1. Automotive Industry
In the automotive sector, injected molded plastic parts are used in everything from interior components to exterior panels. The lightweight nature of molded plastics helps improve fuel efficiency while reducing manufacturing costs.
2. Consumer Goods
Many household items, including kitchen utensils, toys, and appliances, are made using injected molded plastic. This process allows for a variety of shapes and colors, appealing to consumer preferences.
3. Electronics
In electronics, injected molded plastic is used for housings, connectors, and other components that require durability and precision. The electrical insulation properties of plastics make them ideal for this application.
4. Medical Devices
Medical devices often require intricate shapes and strict hygiene standards. Injected molded plastic is widely used due to its ability to produce sterile and reliable medical components.
Understanding the Integration with Metal Fabrication
When combined with metal fabrication, the role of injected molded plastic becomes even more significant. The integration of these two manufacturing techniques can enhance product performance and create innovative solutions.
1. Hybrid Manufacturing Solutions
The combination of metal and injected molded plastic allows for the creation of hybrid parts that capitalize on the strengths of both materials. For instance, a metal core can provide strength while an outer plastic shell offers durability and aesthetics.
2. Cost Efficiency and Weight Reduction
By utilizing injected molded plastic components alongside metal, manufacturers can reduce overall production costs and weight. This is particularly beneficial in industries like aerospace and automotive, where weight savings can significantly enhance performance and efficiency.
Choosing the Right Materials for Injected Molded Plastic
The choice of material for injected molded plastic applications is critical. Various types of polymers can be employed based on the intended use and performance requirements.
Popular Types of Plastics Used
- Polypropylene (PP): Known for its chemical resistance and flexibility, ideal for automotive and consumer products.
- Polyethylene (PE): Offers high toughness and is commonly used in packaging and containers.
- Polyvinyl Chloride (PVC): Versatile and strong, used in construction, plumbing, and medical applications.
- Acrylonitrile Butadiene Styrene (ABS): Known for its strength and rigidity, suitable for electronic housings and toys.
- Polycarbonate (PC): Offers high impact resistance and is used for safety goggles and electronic components.
The Future of Injected Molded Plastic in Manufacturing
As technology advances, the future of injected molded plastic in manufacturing looks promising. Innovations such as sustainable materials, smart manufacturing techniques, and enhanced recycling methods are set to transform the industry.
1. Sustainable Practices
With growing environmental concerns, manufacturers are increasingly looking for sustainable materials for injection molding processes. Bioplastics and recycled plastics present eco-friendly alternatives that can reduce carbon footprints across industries.
2. Technological Advancements
Emerging technologies such as 3D printing and automated processes are enhancing the capabilities of injected molded plastic. These advancements are simplifying production, reducing costs, and improving design flexibility.
3. Customization and Personalization
The demand for customized products is on the rise. As manufacturers adopt injected molded plastic, they will be better equipped to offer personalized solutions that meet specific consumer needs and preferences.
Conclusion
In conclusion, injected molded plastic plays a crucial role in modern manufacturing, particularly in the realm of metal fabrication. Its benefits, including efficiency, versatility, and cost-effectiveness, make it an essential technique for businesses looking to innovate and enhance their product offerings. Companies like DeepMould.net, specializing in metal fabrication, can leverage the advantages of injected molded plastic to stay competitive in today's fast-paced market.
As industries continue to evolve, the synergy between injected molded plastic and metal fabrication will undoubtedly pave the way for groundbreaking products and solutions. By embracing this technology, manufacturers can position themselves at the forefront of the industry, driving innovation and delivering exceptional value to their customers.